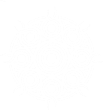
Handpan vs tongue drum
Handpan or togue drum? This is one of the most frequently asked questions that we face every day, many people want to know what are the differences between these two instruments and which one fits their needs better. In this article, we are going to provide some points in this regard.
Basically, in spite of some similarities, they are two totally different musical instruments. Pantams have more clear tone and magical bright ceramic and smooth sound with mid to high range of sustain (resonate), while tongue drums have more like a blur sound with long sustain. handpans are made with different materials being suitable for different playing styles and environment vibes including indoor fast professional playing to outdoor slow meditative styles, while tongue drums are known for only more slow and meditative playing. Moreover, Handpans can be more flexible than tongue drums, for example you can get up to 22 notes on a Handpan but the notes on tongue drums are limited.
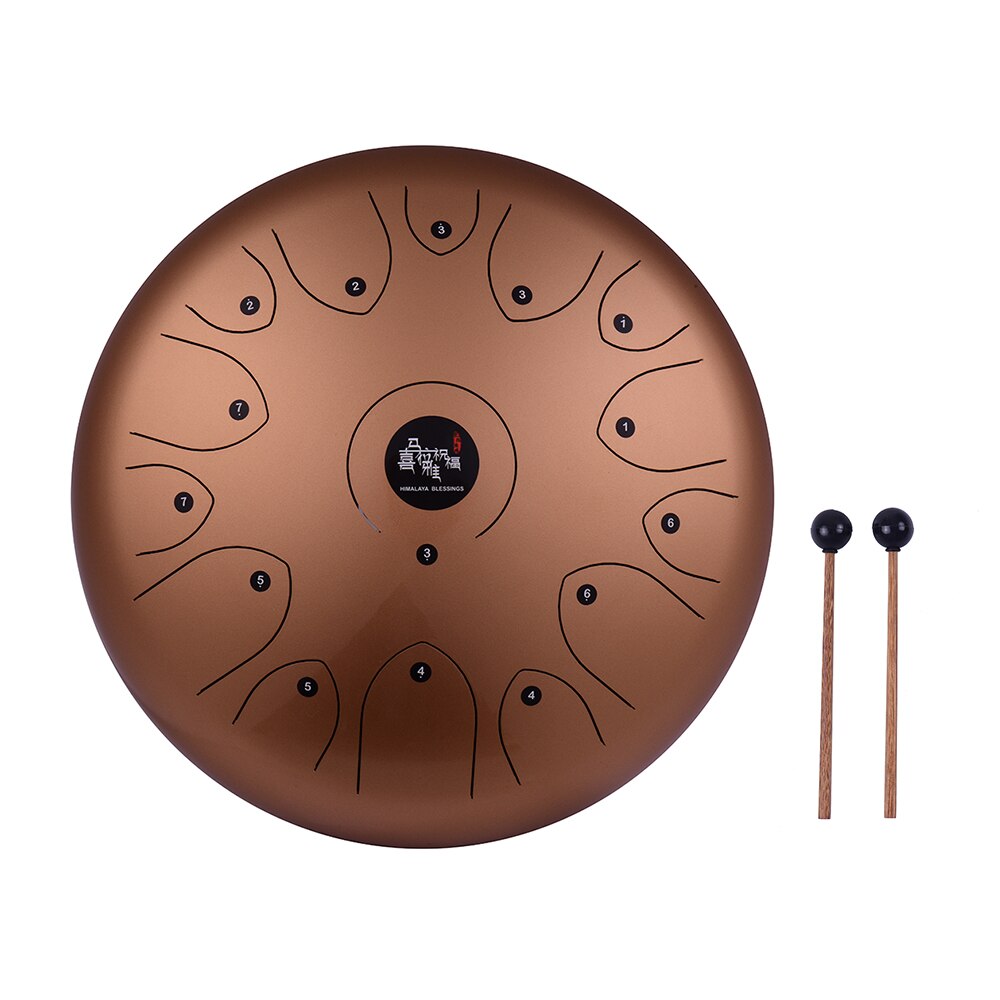

Although Tongue drums are in general smaller in size but much heavier than Handpans (hang drums) since they are made of thicker steel sheets. Besides the Handpans standard size range is 18-23 inches, so sometimes a small Handpan (mini handpan) can be in a size of a tongue drum but still much lighter and having of course a different sound.
Due to the much more complexities in making Handpans, their price is much higher than the tongue drums, but as mentioned at the beginning, these two are totally different instruments and paying less doesn’t mean you will be able to get the same thing.
Tone Fields
This is where handpans and tongue drums become different in a noticeable way. The tone field or the notes that you play will look completely different. The handpan containing dimples and dings, with no piercing of the steel, while the steel tongue drum tongues will be cut into the steel, in a variety of shapes.
Overall, Handpans and tongue drums comparison seems like comparing apple and orange, both round and almost same shape but completely different fruits with different taste and nutrition. We want to say, if you are interested in Handpans, then you should get one and never think that you will be able to get something similar while spending less. Likewise you might be interested in tongue drums and again in this case a Handpan cannot be an alternative.
We hope you find these information useful and this article can help you decide if you are thinking between a Handpan and a tongue drum.If you know that you want a high quality Handpan with a fair price, please visit our available instrument page to see our latest available instruments for sale. If you have any questions, please don’t hesitate to ask, you may contact us via the contact form below or send an email to [email protected]. Stay tuned


For more information, please visit our Makers Shop page or contact us at [email protected]
stay tuned for further notice, our team has some amazing news for handpan lovers.
Tags
- handpan, Handpan vs tongue drum, hangdrum, pantam, tongue drum